Quality Assurance vs Quality Control: What's the Difference?
- apergnik
- Jan 15, 2024
- 6 min read
Quality assurance and quality control are two terms that may sound very similar, but the two concepts are not exactly the same. Understanding the difference between the two is important to harness the full benefit of both. Although they are similar, and sometimes used interchangeably, they are two different ways of ensuring consistent levels of quality are delivered in products and services. There are multiple factors that distinguish each practice from the other, and it's useful for businesses across a range of industries to have a good grasp of them.
At their core, quality control (QC) involves checking products after production and quality assurance (QA) focuses on developing the right processes to keep production quality high. The two fields are connected and should be considered together but they shouldn't be treated as exactly the same thing. Once you understand how they differ, you can ensure you approach them in the right way.

What Is Quality Assurance?
According to ISO 9000, the international standard for quality management systems, quality assurance is "focused on providing confidence that quality requirements will be fulfilled". So the focus of quality assurance is putting the right processes in place to produce a quality product or service. Quality assurance aims to prevent any mistakes and ensure that things are done right the first time, hence it can be said that it has a proactive approach. It manages quality by defining essential processes, strategies and policies, as well as setting standards that should be followed.
Some of the activities that could be involved in quality assurance include:
Drawing up quality control plans and creating protocols for documentation
Delivering employee training to ensure high quality standards
Auditing internal quality assurance procedures
What Is Quality Control?
Whereas quality assurance is about how quality requirements will be fulfilled, the international standard defines quality control as "focused on fulfilling quality requirements". Quality control is about reviewing the factors involved in production to determine their quality. Whereas quality assurance aims to prevent mistakes, quality control focuses on identifying and fixing defects after they have occurred. Products are inspected to determine whether they meet quality requirements so that they can be corrected if necessary, or perhaps removed from the production line.
When carrying out quality control, some actions that are performed might include:
Testing products after production
Carrying out inspections in manufacturing plants during the production process
Carrying out audits of the entire manufacturing process
How Are Quality Control and Quality Assurance Similar?
Both quality assurance and quality control are part of a comprehensive quality management system. That means they are interlinked and both help to produce products or services that meet the standards that the business wants to set. The two terms are sometimes used interchangeably because they cover similar areas, indicating the ways the two practices are often viewed as being inextricably linked. However, it's still important to recognise that there are also many differences between quality control and quality assurance.
There are several key similarities between quality control and quality assurance, and their overall goals. Firstly, both help to maintain a high-quality product in different ways. While quality assurance involves strategising how to maintain quality, quality control checks that the finished product meets expectations. Another similarity is that both QA and QC follow standards set by the business to obtain the best results. Quality assurance has a greater focus on processes, but quality control also requires following set rules and procedures to determine quality.
One of the overall goals of quality management is to prevent problems and prevent unnecessary expenses. This means that both QA and QC need to contribute to this goal, which they do in different ways. Quality assurance helps to prevent defects during the manufacturing process, while quality control catches them in the finished product before it can be rolled out. The processes and procedures put in place for QA and QC help to improve how all products are made across the business.

How Do Quality Control and Quality Assurance Differ?
Although there are some similarities between quality control and quality assurance, that doesn't make them the same. There are multiple differences that are important to note when engaging in either field.
The overarching goal of both QA and QC might be to ensure quality products, but they each have different goals too. Quality assurance focuses on the production process, implementing processes that will help to ensure a quality product at the end of production. Meanwhile, quality control is more focused on reviewing the final product to detect any defects. Of course, these two goals can be linked. If testing a final product highlights a flaw that needs to be corrected, it could lead to changes in quality assurance processes. Ultimately, they share the same goal of maintaining high standards, but they achieve this goal in different ways.
Because they have different goals, quality assurance and quality control obviously involve different practices too. Quality assurance creates processes and procedures to maintain quality during production, including training employees to maintain high standards. Quality control carries out testing and assessments of final products and may also include carrying out inspections and audits during production.
The time spent on quality assurance and quality control typically differs too. Quality assurance is a longer process that is carried out before production and during the production process. Meanwhile, quality control tends to be a shorter process that largely takes place once production -or a certain step in the production process- is complete. Quality assurance professionals might spend a lot of time developing procedures before the production of a new product begins and they might continue to ensure the correct processes are implemented both during and after production. Quality control may focus more on checking the final product once production is completed, with some steps to check quality during production too.
Quality control and quality assurance experts will have different responsibilities relating to ensuring high standards. Quality assurance might be responsible for setting standards and implementing policies for quality control to carry out, while quality control professionals need to ensure all products meet the set standards before they can leave the factory.
Examples of Quality Control
There are many methods and techniques that might be used in quality control to ensure the quality of a final product. For example, some of the methods used in manufacturing might include inspecting parts at each workstation, Statistical Process Control (SPC) and inspection of finished products.
In the aerospace industry, quality control can include steps such as mechanical testing, incoming material inspection, physical-chemical testing, and non-destructive testing.
Meanwhile, in the energy industry, quality control procedures could include testing energy systems, devices and components, following best practices for installation, and monitoring the variability of renewable resources and their impact on the energy grid.
The exact methods used for quality control can vary by industry, as well as differing from one organisation to the next. It's important for businesses to develop their own quality control processes to ensure they deliver products that meet their standards.
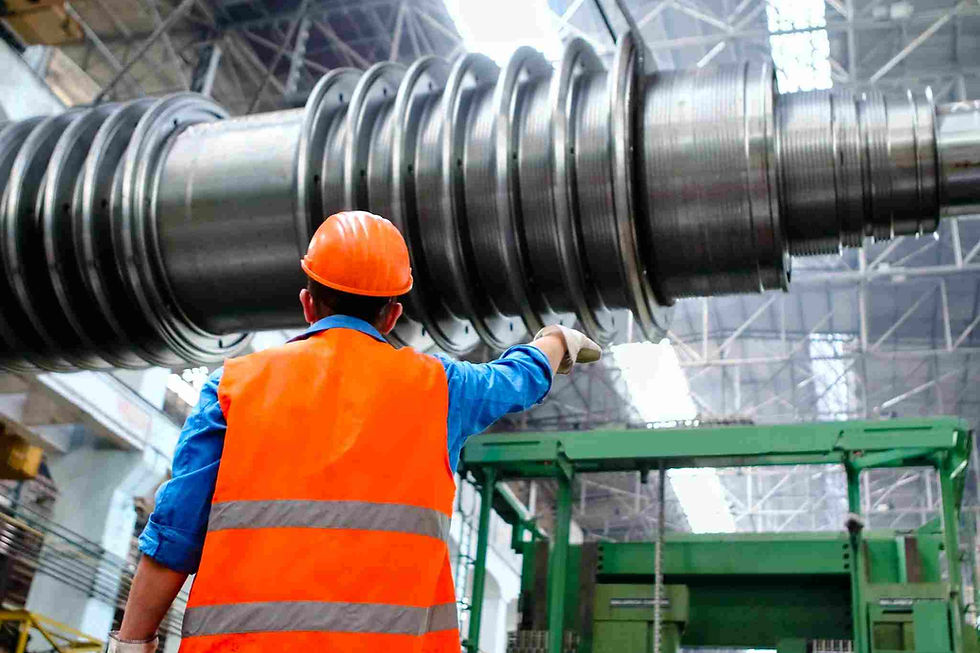
Examples of Quality Assurance
There are also many different ways quality assurance might be implemented as part of a quality management system. In manufacturing, monitoring and fixing problems that could affect the quality of a product is an important part of carrying out quality assurance. Quality assurers need to design processes that help to ensure quality products, making adjustments to their processes and strategies as needed. Working together with quality control teams, they can identify any problems that might need to be addressed before or during the production process.
A detailed example is the occurrence of human error, which can be a major concern in various industries. Quality assurance professionals in industrial technical services play a crucial role in idenitfying and reducing instances of human error. They can achieve this through staff training and implementation of other measure, such as the use of precise tools and automation in the production process, as well as in the finished product. They establish processes during manufacturing to minimize -or completely eliminate- the possibilities of human error and ensure higher quality.
How to Implement Effective QA and QC Processes
Both quality assurance and quality control need to operate within a wider quality management system. To set effective processes for QA and QC, it's important to think about how they connect to each other and contribute to the overall quality management programme. Experienced firms in the management and consulting services sector can offer valuable advice.
Before implementing the right processes, it's necessary to carry out assessments to determine which processes should be put in place. What are the crucial parts of the production process or delivery of the product or service that could affect the quality of outcomes?
For instance, CTQ, also known as Critical to Quality, is a fundamental principle in quality management that identifies the essential characteristics of a product or service that must be present in order to meet the requirements of customers. It converts customer expectations and needs into measurable parameters that guide the production process to ensure that the final result aligns with the customer's expectation and perception of high quality.
The next step is to develop quality planning and control processes and implement inspection and testing. QA and QC need to balance preventive methods to maintain quality with methods for correcting any errors that are detected. Understanding the difference between quality assurance and quality control will make it easier to approach this in the right way.
When considering quality assurance vs quality control, recognising that they are different is essential. But it's also useful to consider their similarities and remember that they have the same overall goal of achieving high standards in all products that are created. They need to work together as part of overall quality management.
Struggling with quality in manufacturing? We are here to help! Take advantage of our exclusive offer: a FREE initial consultation! Don't hesitate to contact us now at info@alphacron.co.uk or call us on 0333 772 2996 to learn more.