
Excellence in Engineering Project Management - A Case Study
Delve into our case study showing the crucial role of our project management service in an engineering and manufacturing project for a gas turbine engine.
Introduction
This case study presents the journey of an innovative transition of a gearbox seal for a gas turbine engine. The project, initiated and led by our project manager, necessitated a strategic redesign of the seal, the implementation of a new manufacturing process, and rigorous validation testing.
Background
The gearbox seal, serving as an oil/air seal, played a vital role in preventing oil leakages by utilising air pressure. The seal was initially produced through the investment casting process, due to the presence of a unique oil drain feature, which necessitated a process that could handle its complex shape. However, the casting process exhibited certain limitations, including issues of porosity and high costs, which prompted the need for a more robust and cost-effective manufacturing process.
Review of service experience and evidentiary data revealed that the oil drain feature was redundant, which led to the decision to remove this feature, enabling a shift to the more robust and cost-effective manufacturing process: machined from forging.
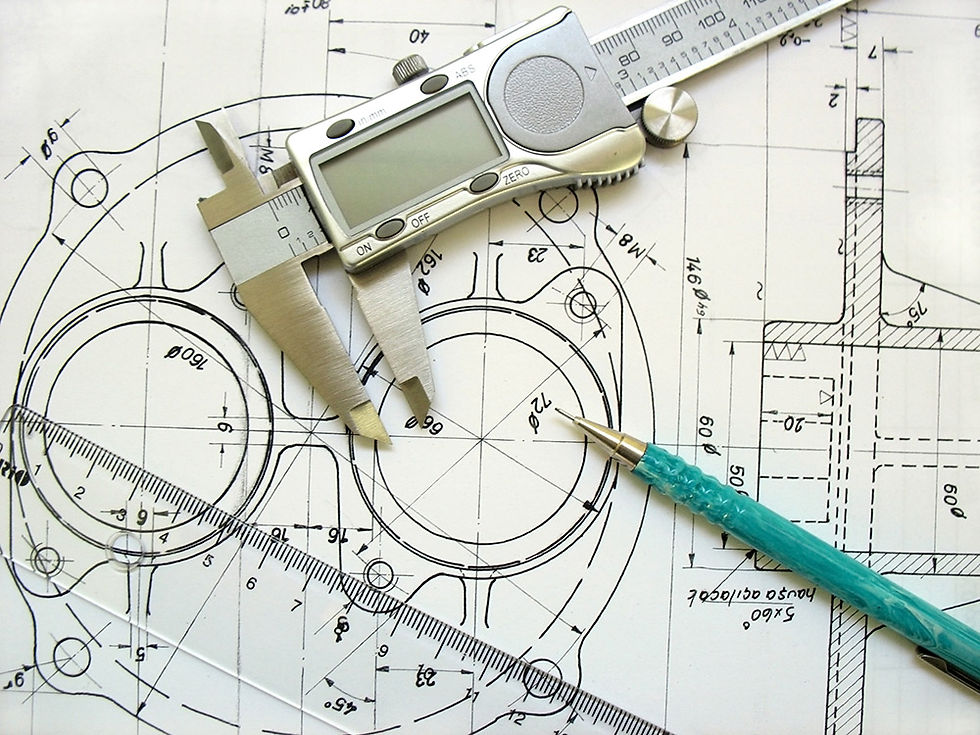
The Project Governance Process
The transition from casting to machined forging was carried out in a systematic manner utilising project management principles, following a "gated" process. This process, overseen by our project management consultant, involved distinct stages, each marked by a "gate" that could only be passed once specific criteria were met.
Idea Generation: The first stage involved identifying the need for change and generating the idea of transitioning from machined-casting to another manufacturing process. The generation of a viable business case was also important. This stage required a thorough analysis of the existing process and its limitations, as well as an exploration of alternative manufacturing methods. At this stage it was determined that the benefits of the project would be realised if the component was going to be produced from forging (machined from forging).
Supplier Selection: A significant part of the project manager's role involved overseeing procurement. Out Project Manager was instrumental in aiding our client down-select potential external suppliers, including forgers and machinists. After a rigorous selection process involving three potential suppliers, the project manager led a technical and financial review that resulted in the selection of the most suitable external supplier for forging and another for machining.
Redesign of the Component (seal): Once the idea was approved and potential suppliers were identified, the focus shifted to redesigning the seal to accommodate the machined forging process. This redesign had to ensure that the seal was able to meet all the requirements and that primarily it could effectively utilize air pressure to prevent oil leakages. There were several specialist functions involved in the redesign process. For instance. the material alloy was different as it was forged and not cast, hence its properties were different compared to the baseline design. A materials expert had to underwrite the chosen material. Other specialist functions involved and approved the redesign of the component were: Bearings Engineer, Air Systems Engineer, Stress Analysts, Component Definition Modellers, Oil Systems Engineers, Weights Engineer and Thermals Engineer.
Process Development: In parallel with the redesign procedures, the manufacturing process had to be developed to incorporate the new process: machined-forging. This stage involved the development of new operational procedures with a new external supplier, the procurement of necessary equipment, and workforce training. One key aspect of our project manager's role was the application of the Production Part Approval Process (PPAP) during this stage.
Validation: After the manufacturing process was developed and trial parts were produced, a modal test was carried out as a validation measure. This test confirmed that the new component was able to withstand the vibration and stress levels during various operational circumstances of the gas turbine engine. Data from the test was compared with similar data from the original design of the component. Overall, the effectiveness of the new process and the superior performance and durability of the redesigned seal was proven at the validation stage.
Incorporation to Engines: Once validated, the transition to 'machined-forging' part was completed with its incorporation into the production line. The final stage involved the successful integration of the modified seal version on the engine. This activity involved careful planning with the production managers and material resource planners to ensure the production line remained uninterrupted whilst the transition was taking place.

Role of the Project Management Consultant
The entire project was initiated and led by our project manager, who showcased exemplary project management expertise across all functions. The project manager developed and maintained the business case for this project, regularly updated the client, and ensured that the project stayed on track. Our project manager's leadership and expertise across all functions, particularly in the technical and procurement areas as well as clear communication with the client, were instrumental in this successful project.
In total, our Project Manager managed a core project team of 10+ members across 3 different countries and timezones. 27 stakeholders were identified as key contributors or with significant interest into this project.
Overall, our management consultancy played a pivotal role in orchestrating this project. We facilitated the idea generation process, guided the redesign phase, led the developing of the new manufacturing process, and oversaw the validation and implementation and stages. Our expertise ensured a smooth transition, successful validation, and efficient incorporation of the new oil/air seal into thegearbox of the engine.
Conclusion
This transition from one manufacturing process to another in the production of a gas turbine engine gearbox seal was not only a testament to the power of innovation and adaptability, but also to effective project management. The project resulted in a superior, cost-effective product, highlighting the value of successful project management in the manufacturing industry.
Project Gallery
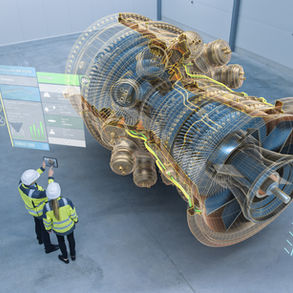